The Labor Rights and Business Case for Factory Audits and Advising
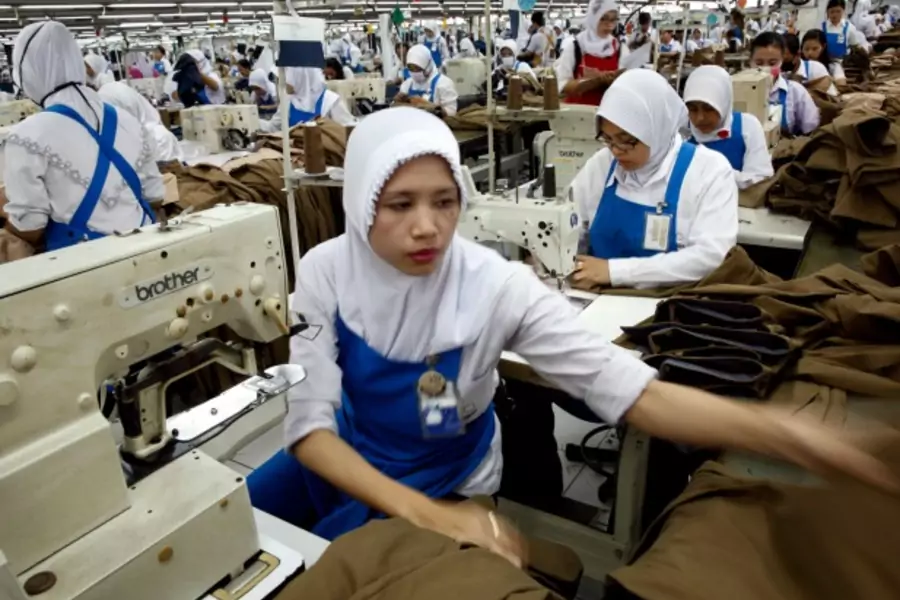
More on:
Global trade and the supply chains that support it are undergoing a period of profound change. Supply chains face threats including a resurgence of protectionism, climate change, decaying infrastructure, and human rights abuses. The Development Channel’s series on global supply chains highlights experts’ analysis on emerging trends and challenges. This post is from Drusilla Brown, associate professor of economics at Tufts University and director of Tufts International Relations Program.
Auditing workplaces in global supply chains is often rejected both as ineffective in improving conditions and as a superficial attempt to salvage the reputation of global brands. But new research shows auditing improves the lives of workers on its own and is particularly effective when paired with supervisory skills and worker empowerment training. Benefits to workers can be achieved without hurting a company’s bottom line—and may even improve it.
Better Work is a joint initiative by the International Labor Organization and the International Finance Corporation that aims to improve work conditions in developing countries by auditing and advising factories. My research colleagues and I were asked to evaluate the program’s effectiveness in seven countries: Cambodia, Haiti, Indonesia, Jordan, Lesotho, Nicaragua, and Vietnam. To do so, we gathered data on firms’ revenue and production, surveyed workers and their managers, and randomly assigned factories to varying amounts of program exposure. While the data varied country-by-country and firm-by-firm, the trend was clear: Better Work factories had more humane labor practices as perceived by workers and were more profitable.
Surveys revealed that workers in Indonesia were less concerned with accidents and injuries; workers in Vietnam were less likely to report fatigue, stomach pain, and chemical smells; and in Jordan they were less likely to report headache, fatigue, hunger, thirst, and risk of injuries. Verbal abuse and sexual harassment significantly declined in all three countries and evidence of human trafficking declined in Jordan. Employees in Vietnam also said they work fewer hours and receive their full pay, clocking about three and a half hours less and earning over $7 more per week. We found similar results in Jordan and Indonesia.
Businesswise, many firms became more productive as verbal abuse and harassment declined. Following a supervisory skills training program, worker turnover fell and productivity rose an average of 22 percent. Improvements arose from training that encouraged supervisors to take the perspective of workers and employ positive motivational techniques.
Factories receiving Better Work services in Vietnam boosted revenue relative to cost an average of 24 percent after four assessment cycles. The services also helped expand business, with international brands placing larger and more regular orders with partners who had improved working conditions.
Those factories meeting basic labor standards also prove to be more resilient during financial downturns. In Cambodia, firms that chose compliance after the second assessment were less likely to close than noncompliant factories during the 2008-09 financial crisis.
Many firms around the world employ traditional workplace practices that dehumanize workers. “Fast fashion” brands force factories to produce on short notice, getting clothes from design to sales floors in a matter of weeks. Under this stress, supervisors are more likely to verbally harass workers or press them to work excessive overtime. And given the uncertainty of future orders, many don’t devote time or energy to change management practices. Yet the evidence shows that it is possible to improve both workers’ lives and companies’ bottom lines when owners and managers adopt labor management innovations.
More on: